AI and IoT-Driven Predictive Maintenance: Revolutionizing Equipment Ma…
페이지 정보

본문
Predictive Maintenance with IoT and AI: Transforming Industrial Operations
Across modern industrial sectors, unplanned machinery breakdowns can lead to costly downtime, safety hazards, and diminished output. Traditional maintenance strategies, such as time-based or corrective maintenance, often fall short in addressing real-time anomalies. Predictive maintenance, powered by the convergence of IoT and AI, is reshaping how industries monitor and maintain assets by predicting issues in advance and optimizing maintenance schedules.
Core Principles of Predictive Maintenance
Predictive maintenance relies on real-time data gathering from connected sensors embedded in machinery to monitor vibration patterns, pressure levels, and power usage. Advanced AI algorithms then analyze this streaming data to identify irregularities and predict potential failures based on past performance and operating conditions. Unlike scheduled maintenance, which follows a fixed timetable, predictive systems adapt in real time to minimize unplanned downtime and prolong machinery life.
IoT’s Role in Data Acquisition
Industrial IoT devices are the foundation of predictive maintenance, collecting detailed metrics from pumps, conveyor belts, and HVAC systems. 5G networks and edge analytics allow real-time data streaming to cloud-based systems, where AI models process vast datasets to detect trends. For example, a vibration sensor on a wind turbine might flag unusual oscillations that indicate bearing wear, triggering an instant notification for preemptive repairs.
AI-Driven Decision-Making in Maintenance
Deep learning algorithms are adept at uncovering hidden correlations in complex data streams. By training on historical data, these models can estimate risk levels with remarkable accuracy. For instance, neural networks might analyze sensor data from a fleet of vehicles to predict component malfunctions weeks or months in advance. Text analytics tools can also analyze repair records to highlight systemic problems and recommend process improvements.
Expanding the Impact of Predictive Maintenance
While minimizing downtime is a primary benefit, predictive maintenance also enhances safety by preventing catastrophic failures in high-risk environments. Additionally, it curtails resource wastage by streamlining inventory management and lowering power usage. For chemical plants, this could mean preventing spills that risk regulatory penalties, while shipping firms might lower fuel costs by optimizing vehicle maintenance during off-peak hours.
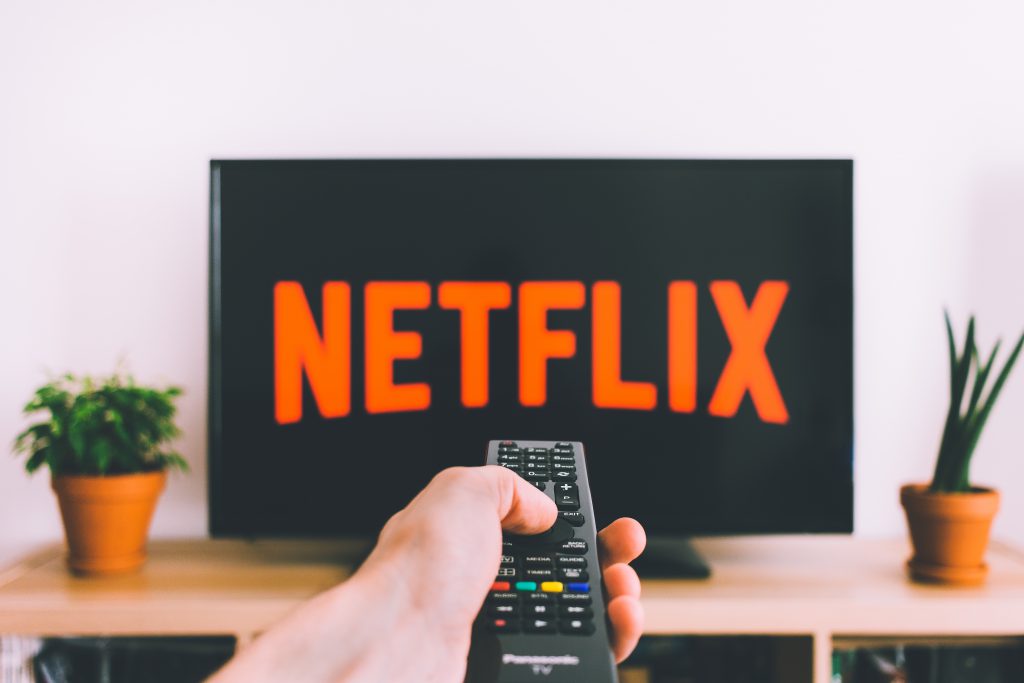
Challenges and Limitations
Implementing proactive systems requires substantial initial costs in sensor networks, data storage solutions, and AI expertise. Many organizations also struggle with connecting older equipment to advanced analytics tools and ensuring data security across connected devices. Moreover, over-reliance on AI predictions can lead to false positives if models are not properly validated or fail to adapt to evolving environments.
Case Study: Predictive Maintenance in Automotive Production
A leading automotive manufacturer recently implemented a predictive maintenance system across its production facilities, equipping robots with thermal sensors and machine learning tools. By processing live sensor feeds, the system detected a persistent calibration issue in paint robots that previously caused hourly downtime. Timely adjustments reduced unscheduled stoppages by nearly 40% and saved the company millions annually.
The Future of Predictive Maintenance
Emerging technologies like digital twins, 5G connectivity, and autonomous repair drones are pushing the boundaries of predictive maintenance. If you liked this article and you would like to receive far more info regarding url kindly pay a visit to the internet site. Digital twin technology, for instance, allows engineers to simulate equipment performance under various scenarios to improve accuracy. Meanwhile, autonomous robots equipped with thermal cameras can monitor remote assets like wind turbines and trigger repair workflows without manual input.
Conclusion
Proactive asset management is no longer a niche solution but a necessity for industries seeking to optimize operations in an increasingly competitive market. By leveraging connected sensors and intelligent algorithms, organizations can transition from downtime management to failure prevention, unlocking significant financial benefits and building resilience in the era of smart manufacturing.
- 이전글How To Create A Weight Training Exercise Workout Program For Women 25.06.11
- 다음글타다라필여성, 비아그라효과없음 25.06.11
댓글목록
등록된 댓글이 없습니다.