AI and IoT-Driven Predictive Maintenance: Revolutionizing Equipment Ma…
페이지 정보

본문
Predictive Maintenance with IoT and AI: Transforming Industrial Operations
In today’s fast-paced industrial landscape, unexpected equipment failure can lead to costly downtime, safety hazards, and diminished output. Traditional maintenance strategies, such as time-based or corrective maintenance, often fall short in addressing dynamic operational challenges. Predictive maintenance, powered by the integration of AI and IoT, is reshaping how industries monitor and maintain assets by predicting issues in advance and streamlining repair workflows.
The Foundation of Predictive Maintenance
Proactive maintenance relies on continuous data collection from connected sensors embedded in equipment to monitor temperature fluctuations, humidity readings, and energy consumption. Machine learning models then analyze this real-time data to detect anomalies and forecast breakdowns based on past performance and environmental factors. Unlike scheduled maintenance, which follows a predetermined schedule, predictive systems dynamically adjust recommendations to minimize unplanned downtime and prolong machinery life.
How IoT Enables Real-Time Monitoring
Smart sensors are the backbone of predictive maintenance, capturing granular data from motors, assembly lines, and HVAC systems. Wireless connectivity and edge computing allow real-time data streaming to centralized platforms, where AI models process terabytes of data to detect trends. For example, a acoustic sensor on a wind turbine might flag unusual oscillations that indicate bearing wear, triggering an instant notification for preemptive repairs.
AI’s Predictive Power: From Data to Insights
Deep learning algorithms excel at uncovering hidden correlations in multidimensional datasets. By learning from past failures, these models can predict failure probabilities with high precision. For instance, decision trees might analyze historical engine performance metrics to predict component malfunctions days or weeks in advance. Text analytics tools can also analyze repair records to identify recurring issues and recommend process improvements.
Expanding the Impact of Predictive Maintenance
While minimizing downtime is a primary benefit, predictive maintenance also improves workplace safety by avoiding hazardous malfunctions in critical infrastructure. Additionally, it curtails resource wastage by streamlining inventory management and lowering power usage. For chemical plants, this could mean preventing spills that risk regulatory penalties, while shipping firms might lower fuel costs by scheduling engine tune-ups during low-demand periods.
Challenges and Limitations
Implementing proactive systems requires significant upfront investment in IoT infrastructure, data storage solutions, and skilled personnel. Many organizations also struggle with integrating legacy systems to modern IoT frameworks and maintaining data privacy across distributed networks. Moreover, over-reliance on AI predictions can lead to false positives if models are not properly validated or struggle to adjust to evolving environments.
Case Study: Predictive Maintenance in Automotive Production
A global carmaker recently deployed a proactive monitoring solution across its production facilities, equipping robots with thermal sensors and machine learning tools. If you adored this article and also you would like to obtain more info concerning Here generously visit our own website. By analyzing real-time data, the system identified a recurring misalignment in paint robots that previously caused hourly downtime. Proactive recalibration reduced unscheduled stoppages by 35% and saved the company millions annually.
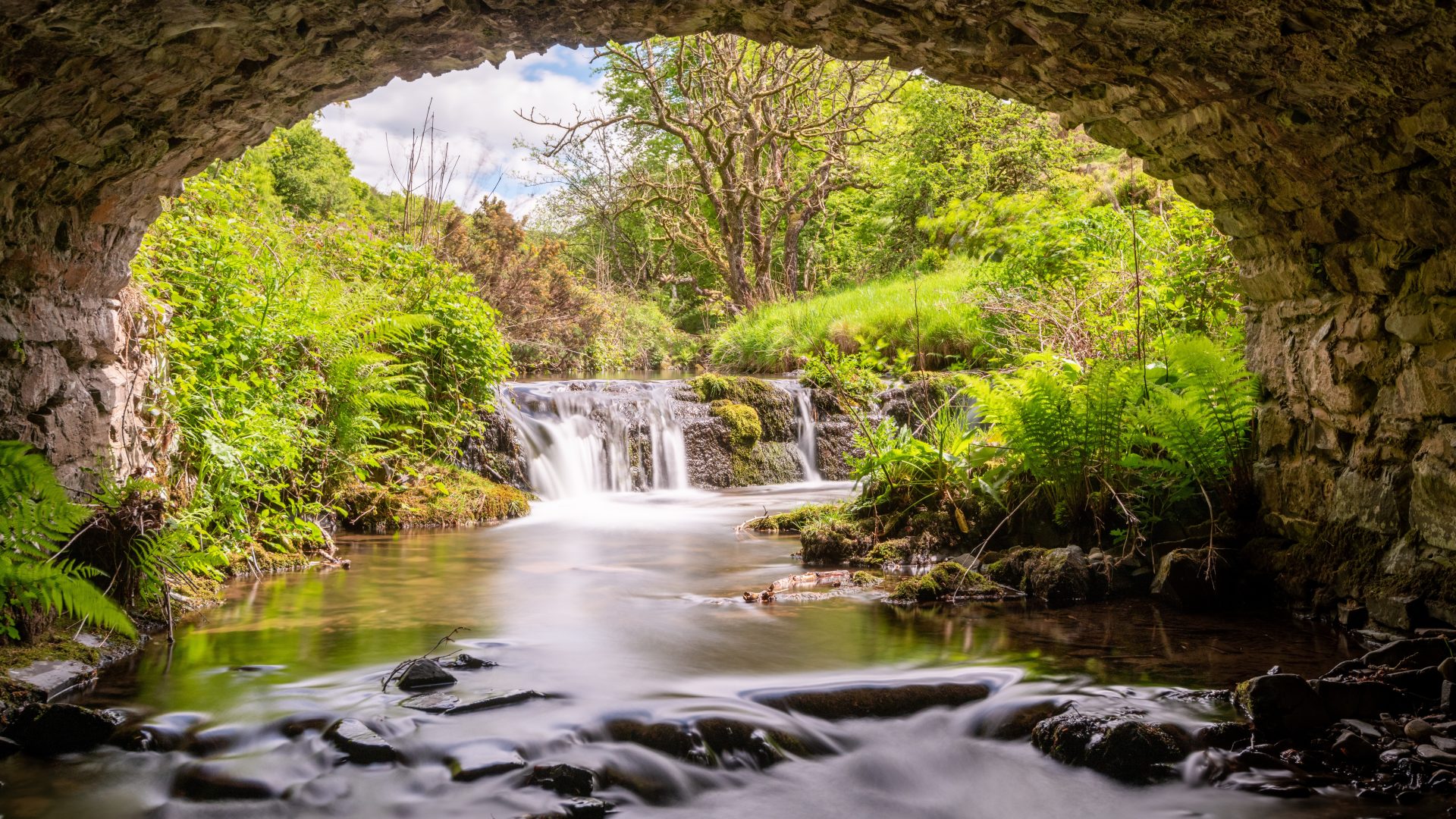
The Future of Predictive Maintenance
Emerging technologies like virtual replicas, ultra-low latency networks, and self-diagnosing systems are expanding the possibilities of predictive maintenance. Virtual modeling, for instance, allows engineers to simulate equipment performance under diverse conditions to refine predictive models. Meanwhile, autonomous robots equipped with ultrasonic sensors can monitor remote assets like wind turbines and trigger repair workflows without manual input.
Final Thoughts
Predictive maintenance is no longer a luxury but a necessity for industries seeking to optimize operations in an rapidly evolving market. By harnessing the power of IoT and AI, organizations can transition from downtime management to failure prevention, unlocking significant financial benefits and ensuring sustainability in the age of Industry 4.0.
- 이전글레비트라 구매 레비트라파는곳 【https://k444.top】 정품카마그라 구입처 정품 시알리스구매 25.06.11
- 다음글레비트라 거래 비아그라인터넷정품구매 25.06.11
댓글목록
등록된 댓글이 없습니다.