Predictive Management with Industrial IoT and AI
페이지 정보

본문
Proactive Management with Industrial IoT and AI
The convergence of Internet of Things (IoT) and machine learning is revolutionizing how industries approach equipment maintenance. Traditional reactive maintenance models, which address issues after they occur, are increasingly being supplemented by data-driven strategies. These next-gen systems utilize real-time telemetry and analytics to anticipate failures before they disrupt operations, reducing downtime and optimizing resource allocation.
At the heart of predictive maintenance is the deployment of smart devices that monitor critical parameters such as heat, vibration, pressure, and power usage. These sensors send data to centralized platforms, where machine learning models process patterns to detect anomalies from baseline performance. For example, a manufacturing plant might use vibration sensors on machinery to detect early signs of component degradation, enabling repairs before a catastrophic breakdown halts the production chain.
One of the key advantages of this methodology is cost efficiency. By anticipating failures, companies can plan maintenance during non-operational hours, avoiding expensive emergency repairs and revenue leakage. A report by McKinsey estimates that predictive maintenance reduces maintenance costs by up to 30% and extends equipment lifespan by 15%. In energy sectors, such as solar plants, this technology prevents unplanned outages that could disrupt power supply to thousands of consumers.
However, implementing predictive maintenance is not without hurdles. The massive amount of data generated by IoT devices requires powerful data storage infrastructure and high-speed connectivity. Industries must also address cybersecurity risks, as sensor networks are vulnerable to hacking attempts. Additionally, integrating AI models with older equipment often demands substantial initial investments in upgrading hardware and training personnel.
Case studies highlight the game-changing potential of this solution. A leading automotive manufacturer reported a 35% reduction in production delays after deploying AI-powered predictive maintenance across its factories. Should you have almost any questions concerning where and also how you can work with locking-stumps.co.uk, you'll be able to e mail us at the site. Similarly, a logistics company leveraged IoT sensors on its vehicles to predict engine failures, slashing repair costs by 18% and improving delivery reliability.
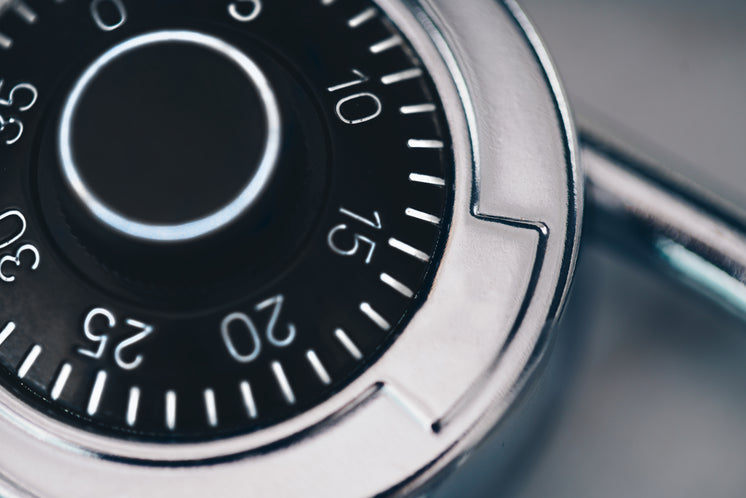
- 이전글비아그라약국판매가격, 정품레비트라, 25.06.12
- 다음글How To Fix Their Car Bicycle Brakes Effectively In Less Time 25.06.12
댓글목록
등록된 댓글이 없습니다.