Proactive Maintenance with IoT and AI
페이지 정보

본문
Proactive Maintenance with Industrial IoT and AI
In the rapidly advancing landscape of industrial operations, organizations are increasingly leveraging innovative technologies to enhance efficiency and minimize downtime. Proactive maintenance, powered by the synergy of the Industrial IoT and machine learning (ML), has emerged as a game-changer for industries ranging from manufacturing to energy and transportation.
The Shift from Reactive to Predictive
Traditional maintenance strategies often rely on fixed inspections or breakdown-based repairs, which can lead to unexpected outages and expensive disruptions. If you have almost any queries with regards to wherever and also how to employ wiki.soholaunch.com, you possibly can e mail us at the web page. In contrast, predictive maintenance uses real-time data from sensors embedded in machinery to track equipment health. Advanced algorithms then analyze this data to forecast potential failures in advance, enabling timely interventions. This data-driven approach lowers maintenance costs by up to 30% and extends the operational life of assets by identifying issues before they escalate.
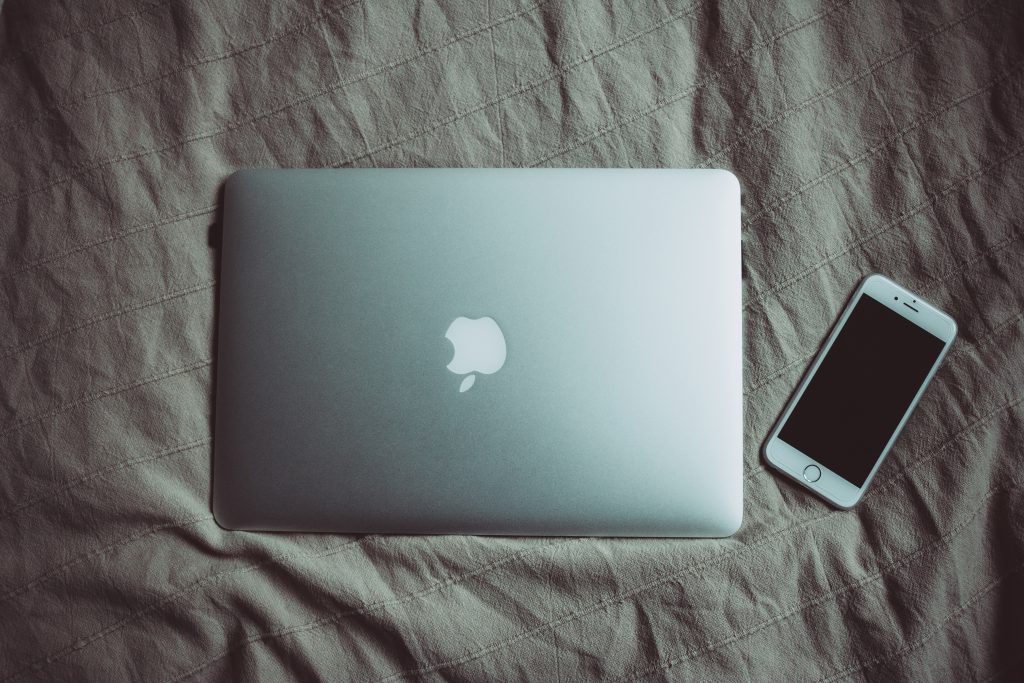
IoT: The Backbone of Real-Time Monitoring
Connected devices are the foundation of predictive maintenance systems. These devices gather vital parameters such as heat levels, vibration, pressure, and moisture from machinery. For example, in a wind turbine, sensors can detect unusual movements that may indicate component degradation. This data is transmitted to cloud platforms for analysis, creating a uninterrupted feedback loop. State-of-the-art IoT networks also support edge processing, where data is analyzed locally to minimize delays and improve response times.
AI and Machine Learning: Turning Data into Predictions
AI algorithms convert raw sensor data into practical recommendations. By training on historical data, these models learn patterns that correlate with equipment failures. For instance, a neural network might detect that a particular sequence of temperature spikes and pressure drops precedes a pump failure. Over time, the system refines its accuracy through ongoing training. Some solutions even employ prescriptive insights, suggesting best maintenance schedules or adjustments to work parameters.
- 이전글시알리스100mg복용법, 시알리스 사용법 25.06.13
- 다음글5 Tips For Personal Stress Management 25.06.13
댓글목록
등록된 댓글이 없습니다.